Bringing ideas to like, one layer at a time
SLA (Stereolithography)
SLA
Stereolithography (SLA) is a sophisticated additive manufacturing technique that leverages a vat of liquid photopolymer resin and a high-powered ultraviolet laser to construct three-dimensional objects layer by meticulous layer. Pioneered in the 1980s, SLA has significantly evolved and is now a prevalent method employed across industries for rapid prototyping, product development, and small-scale production. This technology is renowned for its exceptional precision and ability to produce smooth surface finishes, making it an invaluable tool for high-detail applications.
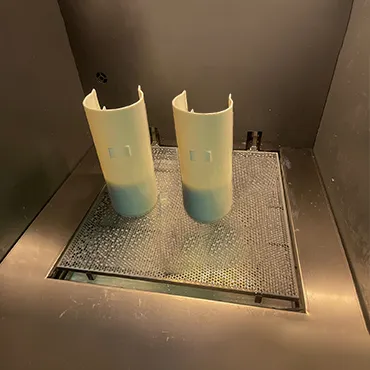
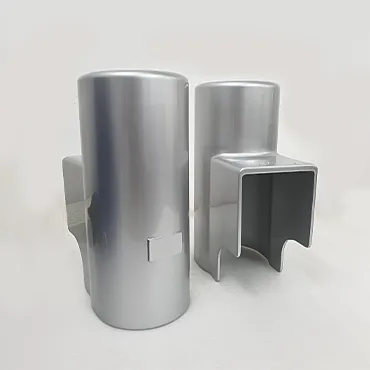
Materials
SLA Opaque (ZR300)
Clear SLA
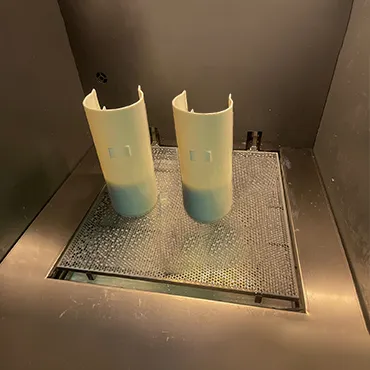
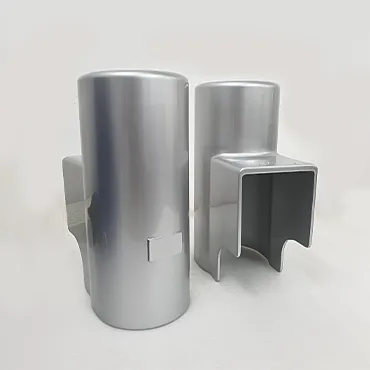
Process Flow :
Preparation
The process begins with digital design data, which is prepared using Computer-Aided Design (CAD) software. The digital model is then sliced into thin layers, generating a series of cross-sectional data.
Material Handling
A powdered material, typically a polymer or a metal, is loaded into the SLS 3D printer's build chamber. The powder is evenly spread across a build platform, forming a thin layer.
Laser Sintering
A high-powered laser scans the cross-sectional data onto the powdered material, selectively melting and fusing the particles together. The laser's energy causes the powdered material to solidify, creating a solid layer of the object being printed.
Layer-by-Layer Building
After each layer is sintered, the build platform moves down, and a fresh layer of powder is spread on top. The process repeats until the entire object is formed, layer by layer.
Cooling and Post-Processin
Once the printing is complete, the object is left to cool inside the printer. Afterward, excess powder is removed manually or using specialized equipment. Depending on the requirements, additional post-processing steps like polishing, dyeing, or surface treatment may be performed.
Advantages :
Design Freedom
SLS enables the creation of highly complex geometries, including intricate internal structures and moving parts, without the need for assembly or additional tooling.
Versatility of Materials
SLS can work with a wide range of materials, including polymers, metals, ceramics, and composites, allowing for the production of parts with diverse properties.
Cost-Efficiency
As SLS does not require moulds or tooling, it eliminates the need for expensive and time-consuming manufacturing setups. This reduces production costs, especially for small batch sizes or customized products.
Time Savings
SLS technology allows for rapid prototyping and quick iterations during the design process, accelerating product development cycles and reducing time-to-market.
Innovative Additive Manufacturing Solutions by RIFTWAY SOLUTIONS
On-Demand manufacturing offers industries flexibility, cost reduction, customization, sustainability and simplifying the supply chain